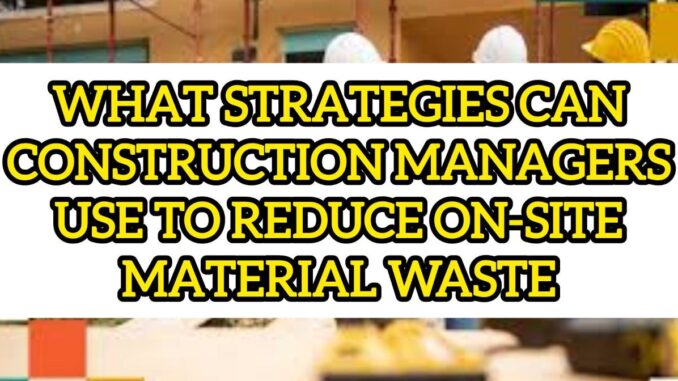
Let’s face it, walking onto a construction site sometimes feels like stepping into a graveyard for perfectly good materials. Piles of off-cut lumber, bent rebar destined for the bin, half-empty bags of concrete hardening in the sun, packaging strewn everywhere… it’s enough to make any cost-conscious or environmentally aware manager wince. It’s not just messy; it’s pure money being thrown away, and it’s hammering our planet unnecessarily. But here’s the kicker: a massive chunk of this waste isn’t inevitable – it’s preventable. As a construction manager, you’re the conductor of this complex orchestra. You have the power, the influence, and frankly, the responsibility, to drastically cut down on this waste. Ready to transform your site from wasteful to wonderfully efficient? Let’s dive into the battle-tested strategies that will make you a waste-whispering warrior.
WHY SHOULD YOU CARE ABOUT CONSTRUCTION WASTE?
Before we get into the how, let’s really hammer home the why. Why does reducing on-site material waste deserve a top spot on your priority list? Think beyond just tidying up:
- Your Profit Margin is Leaking: Every piece of material wasted is money you literally purchased and then threw out. Those off-cuts, damaged goods, and over-ordered supplies? That’s pure profit vanishing. Reducing waste directly boosts your bottom line.
- Ticking the Green Box (For Real): Sustainability isn’t just a buzzword anymore. Clients are demanding it, regulations are tightening, and your company’s reputation hinges on it. Demonstrating effective waste reduction is a powerful green credential.
- Site Safety & Efficiency: A cluttered site is a dangerous site. Tripping hazards, blocked fire exits, inefficient material movement – waste directly contributes to accidents and slows everyone down. A tidy site is a safer, faster site.
- Dodging the Landfill Tax Bullet: Landfill costs are only going up. The less you send there, the less you pay in hefty disposal fees and taxes. Simple economics!
- Resource Stewardship: We’re using the Earth’s resources. Using them wisely isn’t just good business; it’s the right thing to do for future generations. Ever thought about the energy and water embedded in that discarded material?
THE BIG PICTURE: WASTE REDUCTION STARTS BEFORE THE FIRST TRUCK ARRIVES
You can’t just slap a few recycling bins on site and call it a day. Effective waste management is a holistic process that begins long before ground is broken. It requires a shift in mindset – from accepting waste as “just part of the job” to seeing it as a sign of inefficiency to be ruthlessly eliminated.
BUILDING A WASTE-AWARE CULTURE: IT’S A TEAM SPORT
Tackling waste isn’t a solo mission. You need your entire crew, from the architect to the apprentice, singing from the same hymn sheet. How do you foster this?
- Talk About It, Constantly: Make waste reduction a standing agenda item in toolbox talks, site inductions, and planning meetings. Don’t assume everyone understands the why behind the what.
- Educate and Empower: Show crews how their actions contribute to waste (or prevent it). Explain the cost implications in simple terms (“Wasting that bundle of timber costs us $X, that’s like throwing Y hours of your pay away!”).
- Incentivize Smart Thinking: Recognize and reward crews or individuals who come up with great waste-saving ideas or consistently follow best practices. A little positive reinforcement goes a long way.
- Lead From the Front: Your attitude is contagious. If you meticulously sort your own coffee cup, carefully store samples, and question unnecessary orders, your team will notice and follow suit.
PRE-CONSTRUCTION POWER: DESIGN AND PLANNING STRATEGIES
This is where the magic really happens. Stopping waste at the source is infinitely smarter than dealing with it later.
- Embrace VALUE ENGINEERING (The Smart Way): Work with designers and architects early on. Challenge specifications. Can a standard size material be used instead of a custom one requiring tons of cutting? Can a different, less waste-prone system or material achieve the same result? Focus on function and value, not just aesthetics or tradition.
- DETAILED TAKE-OFFS ARE YOUR BIBLE: Garbage in, garbage out. Rushed or inaccurate material quantity take-offs lead directly to over-ordering. Invest the time (or tech – more on that later!) in getting these pinpoint accurate. Double-check, triple-check. Measure twice, order once!
- MODULAR DESIGN & PREFABRICATION TO THE RESCUE: Building components in a controlled factory environment is a game-changer for waste. Precise cutting, reduced damage, minimal on-site storage, less packaging waste, and faster installation? Sign me up! Pushing for more off-site fabrication is a massive strategic win.
- OPTIMIZE FOR STANDARD SIZES: Design to common material dimensions whenever possible. Specifying a wall height that neatly fits full sheets of drywall or plywood eliminates mountains of off-cuts. It seems simple, but it’s often overlooked in the pursuit of unique design.
- MATERIAL SELECTION WITH WASTE IN MIND: Choose durable materials less prone to damage. Consider materials with high recycled content that are also easier to recycle at end-of-life. Investigate suppliers who offer take-back schemes for packaging or unused materials. Think about the entire lifecycle.
ORDERING & PROCUREMENT: GETTING IT JUST RIGHT
This is the critical link between planning and the site. Get this wrong, and waste is guaranteed.
- JUST-IN-TIME (JIT) DELIVERY IS KING: Forget the old-school “pile it high” approach. Coordinate deliveries so materials arrive precisely when they are needed for installation. This minimizes damage from weather, theft, vandalism, and handling. It also frees up valuable site space. Requires great coordination, but the payoff is huge.
- SUPPLIER PARTNERSHIPS ARE GOLD: Don’t just treat suppliers as order-takers. Build relationships. Discuss your waste reduction goals. Can they deliver in reusable containers? Can they take back pallets or packaging? Can they provide materials cut to specific sizes? Can they handle smaller, more frequent deliveries? Good suppliers will work with you.
- THE PERIL OF THE “LITTLE EXTRA”: Resist the temptation to automatically add 10% “just in case” to every order. Base orders on your excellent take-offs and factor in known, predictable waste (like cutting kerf) accurately. That 10% often just becomes 10% waste.
- CENTRALIZED BUYING & STORAGE (For Multi-Site/Project Firms): Consolidate purchasing power and establish a central warehouse for common materials. This allows for bulk buying discounts and efficient redistribution of surplus materials between projects. That leftover pallet of bricks from Job A could be exactly what Job B needs.
ON-SITE MATERIAL MANAGEMENT: YOUR DAILY BATTLEGROUND
This is where your leadership and systems meet the reality of boots on the ground. Execution is everything.
- THE SACRED STORAGE ZONE: Designate specific, well-organized, and protected areas for different materials. Off the ground (on pallets or racks), covered from the elements, secured from theft, and clearly labelled. Organize it logically – first-in, first-out (FIFO) rotation is crucial. Drywall shouldn’t be getting rained on; bags of mortar shouldn’t be buried under lumber. Protect your investment!
- HANDLE WITH CARE (TRAIN, TRAIN, TRAIN!): So much waste is pure damage. Train everyone – from delivery drivers to laborers to tradespeople – on proper handling techniques for specific materials. Use the right equipment (dollies, forklifts, cranes). Don’t drag bundles across rough ground. Don’t overload carts. Treat materials like the valuable assets they are. Make “careful handling” a non-negotiable site rule.
- CUTTING & FABRICATION ZONES: CONTROL THE CHAOS: Establish designated areas for cutting materials. Equip them with proper tools (sharp blades!), measuring aids (lasers, templates), collection bins for off-cuts, and clear signage. Enforce using these zones – no random cutting wherever you feel like it! This concentrates waste, makes collection easier, and allows for potential sorting of reusable off-cuts.
- THE ART OF THE OFF-CUT: REUSE BEFORE YOU RECYCLE: Before that piece of plywood or length of conduit goes in the bin, ask: “Can this be used elsewhere right now?” Create an easily accessible “reuse pile” for common off-cut sizes. Encourage crews to check this pile before cutting into a fresh piece. Small blocking, spacers, temporary bracing – there are often dozens of uses. Make reusing second nature.
- PACKAGING: THE SILENT WASTE CULPRIT: Cardboard, plastic wrap, strapping – it adds up fast. Mandate breaking down cardboard immediately. Provide compact balers if volume justifies it. Designate bins specifically for clean plastic film. Negotiate with suppliers to reduce packaging. Have a clear plan for where packaging waste goes – don’t let it become general site litter.
WASTE SORTING & DIVERSION: DON’T JUST DUMP IT ALL!
Okay, some waste is unavoidable (contaminated materials, certain off-cuts). But sending it straight to landfill should be the absolute last resort.
- ON-SITE SORTING STATIONS: MAKE IT EASY: Place clearly labelled bins or skips for specific waste streams right where the waste is generated (e.g., near cutting zones, demo areas). Common streams: Clean Wood, Metals, Cardboard, Plastics (film/packaging), Concrete/Bricks, Gypsum (drywall), Insulation, Hazardous Waste, General/Landfill. Use pictures and multiple languages if needed.
- EDUCATE ON CONTAMINATION: One greasy sandwich wrapper in the clean wood bin can ruin the whole load for recycling. Constantly reinforce what goes where and why contamination is bad (and costly!).
- PARTNER WITH THE RIGHT WASTE HAULER: Don’t just hire the cheapest skip company. Partner with a waste management provider that prioritizes recycling and diversion. Understand their requirements (bale size, contamination limits) and their capabilities (what materials can they actually recycle?). Get diversion reports – track your progress!
- EXPLORE LOCAL RECYCLING & REUSE OPTIONS: Are there local charities (e.g., Habitat for Humanity ReStores) that take unused building materials? Are there specialized recyclers for specific materials like asphalt shingles or vinyl siding? Do your homework!
- DEMOLITION: PLAN THE UNDOING: Before swinging the first sledgehammer, plan the demolition with waste reduction in mind. This is called Deconstruction or Soft Stripping. Carefully remove reusable items (doors, fixtures, cabinets, lumber) for resale or donation. Systematically sort materials as you demolish. Crush clean concrete and brick on-site for reuse as fill or sub-base if possible. Demolition waste is often the biggest volume – manage it smartly.
LEVERAGING TECHNOLOGY: YOUR DIGITAL WASTE BUSTERS
Embrace tools that make precision and tracking easier:
- BUILDING INFORMATION MODELING (BIM): This is your virtual crystal ball. BIM models allow for incredibly accurate quantity take-offs, clash detection (preventing rework), and visualization of material use and waste hotspots before construction even starts. Use it!
- MATERIAL MANAGEMENT SOFTWARE: Track material orders, deliveries, inventory levels, and locations on-site in real-time. Know exactly what you have and where it is, preventing duplicate orders and loss. Some platforms even integrate with waste tracking.
- DIGITAL TAKE-OFF TOOLS: Move beyond paper plans and manual measurements. Digital tools speed up take-offs and drastically improve accuracy, reducing ordering errors.
- WASTE TRACKING APPS: Use simple apps or spreadsheets to log waste skips/weights by material type. This provides hard data to measure your progress, identify problem areas, and report to clients/stakeholders. What gets measured, gets managed!
MONITORING, MEASUREMENT, AND CONTINUOUS IMPROVEMENT
You can’t manage what you don’t measure. How do you know if your strategies are working?
- SET BASELINES & TARGETS: Start by measuring your current waste generation (e.g., tons per $100k of project value, cubic yards per week). Set ambitious but achievable reduction targets (e.g., 15% diversion rate increase, 20% reduction in lumber waste).
- REGULAR WASTE AUDITS: Periodically physically audit your waste skips. What’s actually in there? How much is recyclable vs. landfill? This identifies sorting errors and problem materials.
- TRACK COSTS: Monitor not just waste hauling fees, but also the purchase cost of wasted materials. This is the real financial impact. Compare waste costs project-to-project.
- REVIEW & ADAPT: Hold regular waste review meetings. What’s working? What’s not? What new challenges have emerged? Use your data and observations to refine your strategies continuously. Celebrate successes!
TACKLING SPECIFIC HIGH-WASTE MATERIALS
Some materials are notorious offenders. Here’s how to tackle them head-on:
- LUMBER: Accurate take-offs, optimized cutting plans (software helps!), designated cutting zones with off-cut reuse bins, JIT delivery, proper storage off the ground and covered, training on handling to avoid breakage. Consider engineered wood products (like I-joists) which often generate less waste than dimensional lumber.
- DRYWALL (GYPSUM BOARD): Order optimal sizes (e.g., 54″ wide for 9′ ceilings), use cutting plans to minimize cuts, designate cutting zones with vacuum collection (reduces dust and collects scraps), enforce careful handling to avoid damage, segregate CLEAN gypsum scraps for recycling (many markets exist). Avoid moisture damage at all costs!
- CONCRETE: Precise ordering based on accurate pours (use technology for volume calc!), use ready-mix with consistent quality to avoid rejection, plan pours efficiently to minimize leftover “tailings,” crush clean leftover concrete on-site for reuse as aggregate if possible. Communicate clearly with the batch plant.
- METALS (Reinforcement, Studs, Conduit): Use detailed bending schedules and prefabricated rebar cages if feasible. Implement strict cutting practices with measurement tools to minimize off-cuts. Segregate all ferrous and non-ferrous metals – they have high scrap value! Reuse off-cuts for small ties or supports. Protect from corrosion.
- INSULATION: Careful handling is paramount – once compressed or torn, it’s often useless. Measure and cut precisely. Store in a dry, protected area. Consider batt insulation that fits standard cavity widths precisely. Segregate clean off-cuts – some types can be recycled.
THE HUMAN ELEMENT: COMMUNICATION AND SUPERVISION
All the best plans fail without execution on the ground. Your role as leader is vital:
- CLEAR ROLES & RESPONSIBILITIES: Who is responsible for overseeing material deliveries? Who manages the storage yard? Who checks the cutting zones? Who monitors the waste bins? Make it crystal clear.
- EFFECTIVE SUPERVISION: Regularly walk the site with waste reduction in mind. Observe material handling practices. Check storage areas. Look at what’s going into the bins. Provide immediate, constructive feedback. Praise good practices publicly.
- OPEN CHANNELS FOR FEEDBACK: The guys on the tools often have the best ideas for saving materials. Create a simple way for them to suggest improvements. Listen and act on good suggestions.
- ADDRESSING SUBCONTRACTORS: Include specific waste management expectations and procedures in your subcontracts. Hold subcontractors accountable for the waste generated by their crews. Provide them with the necessary facilities (bins, storage) and communicate expectations clearly. Make it part of their performance review.
BEYOND THE SITE: CLOSING THE LOOP
True waste reduction looks at the bigger picture:
- MATERIAL REUSE NETWORKS: Explore platforms or local networks for exchanging unused materials with other projects or builders. One project’s surplus is another’s shortage.
- DESIGN FOR DECONSTRUCTION (DfD): Think about the end of the building’s life during the design phase. Using reversible connections, standard materials, and minimizing composite materials makes future disassembly and material recovery much easier. It’s forward-thinking sustainability.
- CIRCULAR ECONOMY PRINCIPLES: Aim to move from a “take-make-dispose” model to one where materials are kept in use for as long as possible. This means designing for durability, reuse, remanufacturing, and high-quality recycling. It’s the future.
CONCLUSION
Reducing on-site material waste isn’t a one-off project; it’s a fundamental shift in how we approach construction. It demands proactive planning, meticulous execution, continuous monitoring, and a deep commitment from everyone involved, starting with you, the construction manager. It requires investing time upfront in design, procurement, and training. It means challenging the status quo and embracing new methods like prefabrication and technology.
The rewards, however, are undeniable: significant cost savings, enhanced environmental credentials, improved site safety and efficiency, better relationships with suppliers and waste handlers, and the genuine satisfaction of running a tight, responsible ship. You’re not just building structures; you’re building a reputation for efficiency and sustainability. You’re proving that doing the right thing environmentally is also the smart thing financially. So, take these strategies, adapt them to your projects, engage your team, and start turning that wasteful graveyard into a model of lean, green construction efficiency.
FAQs
Isn’t implementing all these waste reduction strategies going to slow down my project and cost more money?
This is a common misconception. While there’s an initial investment in planning, training, and potentially setting up systems (like better storage or sorting stations), the long-term savings far outweigh these costs. You save on material purchases (buying less), waste disposal fees (tipping less), potential rework (avoiding errors), and often gain efficiency through better organization and JIT delivery. Many strategies, like accurate take-offs and careful handling, cost nothing but attention and actually speed up the project by preventing delays due to missing/damaged materials or cluttered workspaces.
How do I get buy-in from subcontractors who might see waste reduction as extra work for them?
Include specific waste management requirements in their contracts. Explain the why – cost savings that benefit the overall project (and potentially future bids), a safer site, meeting client sustainability goals. Provide the necessary infrastructure (well-placed, labelled bins, storage space). Offer training on site-specific procedures. Consider incorporating waste performance into their evaluation or even offering small incentives for good compliance. Frame it as part of doing a professional job efficiently.
What’s the single most impactful strategy I can implement quickly?
If you had to pick one, Just-In-Time (JIT) Delivery combined with Protected, Organized Storage offers a massive bang for the buck. It dramatically reduces damage from weather, handling, and theft, minimizes loss from materials being buried or forgotten, and frees up crucial site space. It requires good coordination but delivers immediate, visible results. Pair this with enforcing designated cutting zones for a powerful one-two punch.
How do I actually measure our waste reduction success?
Start by tracking key metrics:
Waste Haulage: Number of skips/roll-offs hauled, their size, and cost (separate landfill vs. recycling if possible).
Weight Tickets: Get weights from your waste hauler for different streams (landfill, wood, metal, concrete, etc.).
Material Purchase vs. Installed: Track the cost and quantity of key materials purchased versus what was actually installed (accounting for design quantities). The difference is your avoidable waste cost.
Diversion Rate: Calculate the percentage of total waste diverted from landfill (recycled + reused). Set a baseline and track improvement.
Use this data to generate simple reports, identify trends, and prove the value of your efforts to management and clients.
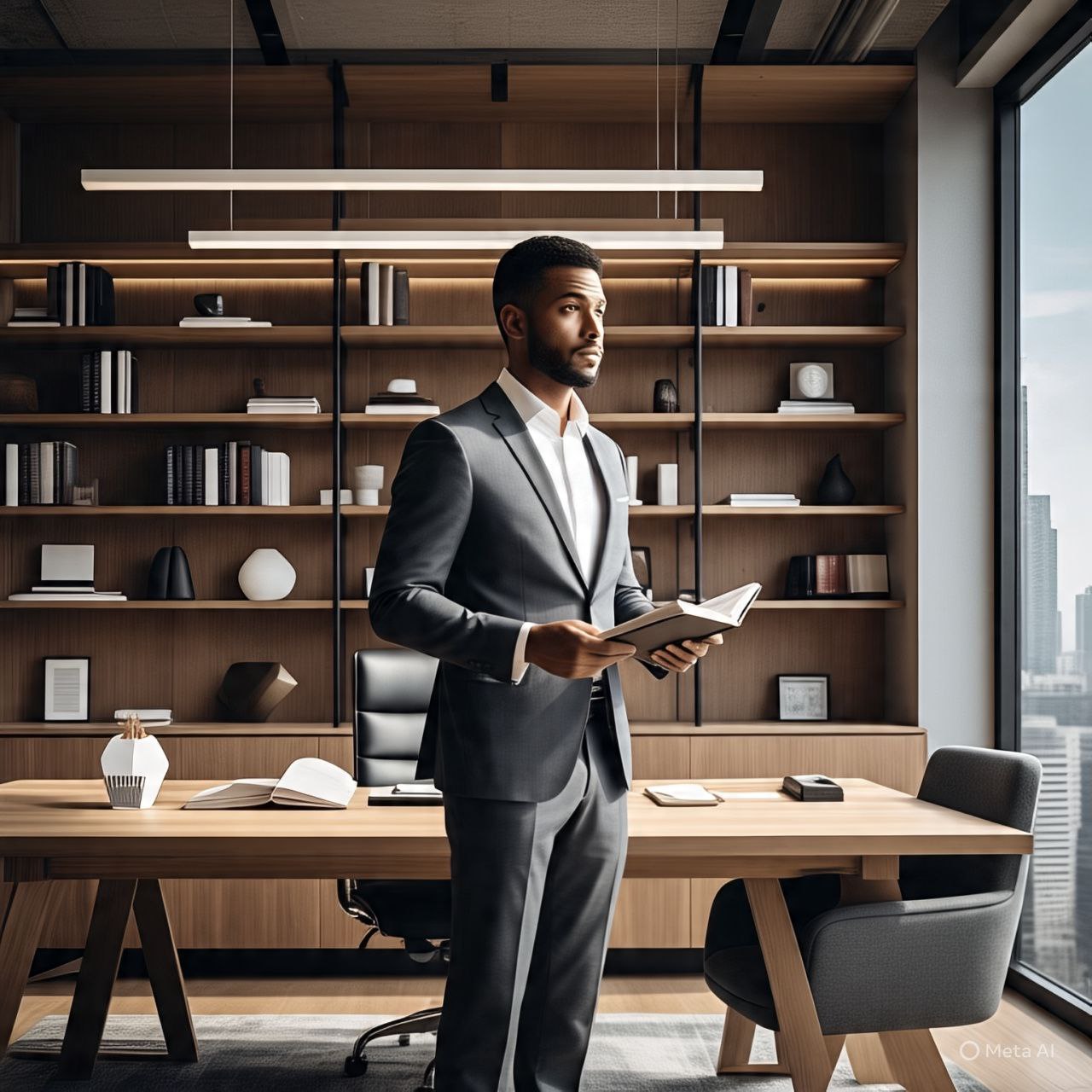
West is both an engineer and a construction manager with a solid ten-year track record in directing building projects and managing their financial aspects. Throughout his career, he has honed his skills in coordinating multidisciplinary teams, streamlining budget processes, and structuring financing plans that ensure projects are delivered on time and within financial targets.
Leave a Reply