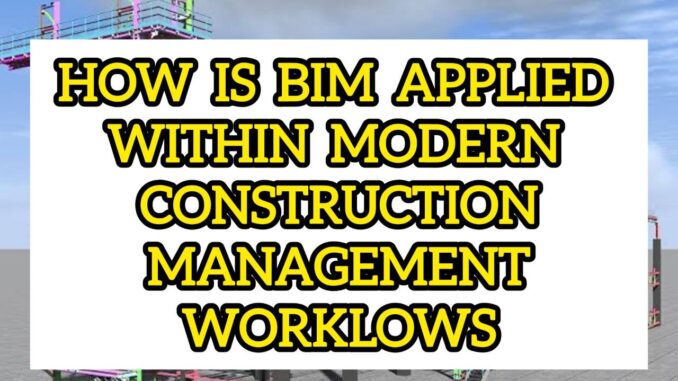
Ever tried to assemble a giant jigsaw puzzle without the picture on the box? That’s what traditional construction can feel like—endless pieces, no clear guide, and the nagging worry that one wrong placement will spoil the whole picture. Building Information Modeling, or BIM, hands you the box top and highlights the edge pieces first. It’s more than just 3D drawings; it’s a living digital twin where every beam, pipe, and thermostat carries its own data tag—cost, material, maintenance schedule, you name it. From initial sketches through demolition decades later, BIM underpins modern construction management workflows, turning a once fragmented process into a seamless, data-driven journey.
What Exactly Is BIM? Beyond 3D Geometry
On its surface, BIM looks like a fancy CAD model, but it’s really a robust database wrapped in geometric skin. Every model element—walls, windows, ducts—carries metadata. Imagine clicking on a pipe in your model and instantly accessing its manufacturer’s specs, lead times, and maintenance manuals. That’s BIM magic: geometry meets information.
The Origins and Evolution of BIM
BIM’s roots stretch back to the 1970s when visionaries sketched “Building Description Systems.” But it wasn’t until the 2000s that computing power and interoperability standards like IFC matured enough to spark widespread adoption. Today, cloud platforms let global teams collaborate on a single model in real time—a far cry from the siloed paper trails of yesteryear.
Core Principles: People, Processes, and Technology
Successful BIM isn’t about the latest software; it’s a trifecta of trained people, well-defined processes, and the right technology. People embrace a collaborative mindset, processes embed model-centric reviews and data validation, and technology—from Revit to Navisworks to BIM 360—provides the digital backbone.
BIM Maturity Levels: From Sketch to Digital Twin
BIM maturity often gets classified in levels. Level 0 is basic CAD, Level 1 mixes CAD and data, Level 2 features coordinated 3D models, and Level 3 envisions a fully integrated, live digital twin accessible to all stakeholders. Many firms today operate at Level 2 but are eyeing the connected, data-rich world of Level 3.
Key BIM Software and Tools
A robust BIM toolkit spans multiple applications:
Revit for authoring architectural, structural, and MEP models;
Navisworks for clash detection and 4D simulations;
Solibri for rule-based quality checks;
Tekla for steel detailing;
and cloud platforms like Autodesk BIM 360 or Trimble Connect as common data environments where models, documents, and issue trackers live in harmony.
BIM in Early Design: Conceptual Modeling and Feasibility
Before blueprints, BIM empowers rapid massing studies—testing building shapes for daylight penetration or wind flow. Tools like Dynamo integrate with Revit to automate thousands of design variants, revealing the best orientation for energy savings. This early insight prevents costly redesigns and anchors sustainability goals from day one.
Interdisciplinary Coordination: Clash Detection Deep Dive
When architecture, structure, and MEP teams work in isolation, spatial conflicts lurk unseen. BIM’s clash detection scans the federated model, generating reports that prioritize issues—say, a duct clipping through a beam. Coordination managers assign each clash to the responsible discipline, track resolutions, and converge on a coordinated model well before steel ever arrives on site.
Quantity Takeoff and 5D Cost Estimation
Counting bricks manually is yesterday’s chore. BIM extracts quantities directly—square footage of drywall, linear feet of piping—and links them to cost libraries. 5D BIM layers cost over 3D geometry, producing budgets that update automatically when designs change. Instant cost feedback shapes design decisions and safeguards against runaway change orders.
4D Scheduling: Animating the Construction Sequence
By tying model elements to schedule activities, 4D BIM creates a time-lapse of your build. Want to know if scaffold deliveries overlap with facade work? Play the sequence and watch conflicts emerge—then adjust orders without juggling countless spreadsheets. This virtual phasing also helps plan site logistics, access, and safety zones.
Site Logistics and Layout Planning
Where do you park the trailers? How much space does material laydown need? BIM’s site layout tools let you place virtual trailers, bins, and cranes on a digital site plan, optimizing traffic flow and minimizing rework. Simulating load-in paths virtually prevents forklift traffic jams in reality.
Prefabrication and Modular Construction
Precision is prefab’s best friend. BIM models drive offsite factories to cut modules, panels, and assemblies with laser accuracy, cutting waste by up to 30 percent. When pieces arrive on site, they snap into place like LEGO, compressing schedules and boosting quality.
On-Site BIM: Mobile Apps and Augmented Reality
Field crews armed with tablets access the latest model in BIM 360 Field, marking up issues, snapping photos, and logging progress against individual elements. Augmented reality (AR) takes it further: headsets overlay digital BIM models onto the physical world, guiding installations with virtual markers that show exactly where pipes or rebar belong.
Quality Assurance and As-Built Validation
At turnover, laser scanners capture point clouds of the built condition. Automated comparison tools highlight deviations from the design model—beams out of tolerance or misaligned conduits—so corrective work happens before handover. This rigorous QA ensures the digital twin mirrors reality, setting facility managers up for success.
Safety Planning and Virtual Hazard Analysis
BIM isn’t just about structure; it’s about safety. Virtual simulations of crane lifts, scaffolding erection, or work at height highlight collision risks and pinch points. These digital hazards feed into toolbox talks, ensuring field crews are primed for safe execution.
Sustainability and Energy Analysis
Energy modeling tools integrated with BIM geometry predict heating loads, daylighting levels, and solar gains. During design charrettes, you can tweak insulation values or window-to-wall ratios and see energy use update on the fly. This data-driven approach steers buildings toward net-zero goals rather than retrofitting green measures post-construction.
Facility Management: The Lifecycle Value of BIM
When the shovel hits the dirt, BIM’s benefits should persist for decades. Handover models carry asset information—maintenance schedules, spare-part numbers, warranty dates—into facility management systems. Technicians navigate the digital twin, locating equipment by clicking on 3D objects rather than rifling through cabinets of paper manuals.
Data Management: Common Data Environments and Version Control
A robust Common Data Environment (CDE)—whether BIM 360 Docs, Aconex, or other platforms—becomes the project’s nerve center. All stakeholders access current models, drawings, and issue logs in one place. Version control tracks every save, ensuring you can revert to prior states if something goes awry. It’s the single source of truth that eliminates outdated prints and email confusion.
Standards and Protocols: ISO 19650 and Beyond
Consistent tagging, naming conventions, and classification systems keep models navigable. ISO 19650 provides a global framework for information management: defining roles (Information Manager, BIM Manager), data exchange protocols, and documentation requirements. Adhering to these standards prevents “wild west” modeling where no two files share the same language.
Building a BIM Execution Plan (BEP)
A BEP lays out the Who, What, and How of BIM on your project: project goals, deliverables, software platforms, model LOD (Level of Development) requirements, coordination schedules, naming standards, and responsibilities. It’s your project’s BIM playbook, ensuring every team knows where to find files, how to name objects, and when to converge on federated models.
Training and Change Management
Even the best BIM strategy stumbles without trained people. Role-based training—modelers mastering Revit families, project managers interpreting dashboards, field crews using mobile apps—fosters confidence. Pilot projects and BIM champions accelerate cultural buy-in, while continuous learning programs keep skills aligned with evolving tools.
Overcoming Common BIM Adoption Challenges
Data overload, hardware bottlenecks, and cultural resistance often derail BIM efforts. Mitigation starts with a phased rollout: pilot on a smaller project, refine your BEP, then scale up. Invest in mid-range workstations, cloud rendering services, and lean modeling to keep performance snappy. Recognize and reward early adopters to spread enthusiasm.
Measuring BIM ROI: Metrics That Matter
Demonstrate BIM’s value by tracking metrics like reduced RFIs, fewer on-site clashes, percent of prefabricated components, schedule compression, and post-handover maintenance costs. A simple dashboard comparing these KPIs pre-BIM and post-BIM delivers a compelling business case for continued investment.
Case Study Spotlight: A Real-World BIM Triumph
Take the Hillside Medical Center renovation: by federating architecture, MEP, and structural models, the team caught 1,200 clashes before breaking ground. Prefabricated mechanical shafts cut installation time by six weeks, and 4D sequencing shaved two months off the schedule. Post-occupancy, technicians used the as-built BIM model to reduce emergency maintenance response by 40 percent.
The Future of BIM: AI, IoT, and Digital Twins
Looking ahead, artificial intelligence will automate clash resolution, suggest model improvements, and even generate initial designs based on performance criteria. Internet of Things (IoT) sensors will feed live data back into the digital twin—tracking temperature, occupancy, and energy use in real time. Blockchain could secure version histories and contractual agreements. Ultimately, we’ll blur the line between BIM and Facility Management, operating buildings in a continuous feedback loop of optimization.
Conclusion: BIM as the Backbone of Modern Construction
Building Information Modeling isn’t a passing trend; it’s the connective tissue binding design, construction, and operations into one coherent lifecycle. From early feasibility studies through facility maintenance decades later, BIM injects data-driven clarity, reduces waste, and elevates collaboration. Yes, it demands investment—in software, hardware, and people—but the payoff is a resilient, agile construction workflow ready for today’s challenges and tomorrow’s innovations.
FAQs
What is the difference between 3D CAD and BIM?
3D CAD represents geometry only—a virtual shape without data. BIM enriches each element with metadata (cost, material, schedule), turning geometry into actionable information across the project lifecycle.
How do I start implementing BIM in my firm?
Begin with a pilot project: define clear goals, create a BIM Execution Plan, train a small core team, and measure results. Use this success to build internal champions and scale to larger projects.
Can smaller contractors benefit from BIM?
Absolutely. Even simple 3D models with embedded takeoff data and clash detection can cut waste and errors. Cloud-based BIM platforms offer pay-as-you-go plans, eliminating hefty upfront costs.
What are common pitfalls to avoid in BIM adoption?
Avoid “model bloat” with unnecessary detail, skip unclear BEPs, under-train staff, and ignore data standards. Phased rollouts, strong governance, and continuous training keep BIM on track.
How does BIM support sustainability efforts?
BIM’s energy modeling tools simulate building performance—daylighting, HVAC loads, solar gains—during design. This upfront insight steers material choices, facade orientation, and system sizing toward net-zero goals.
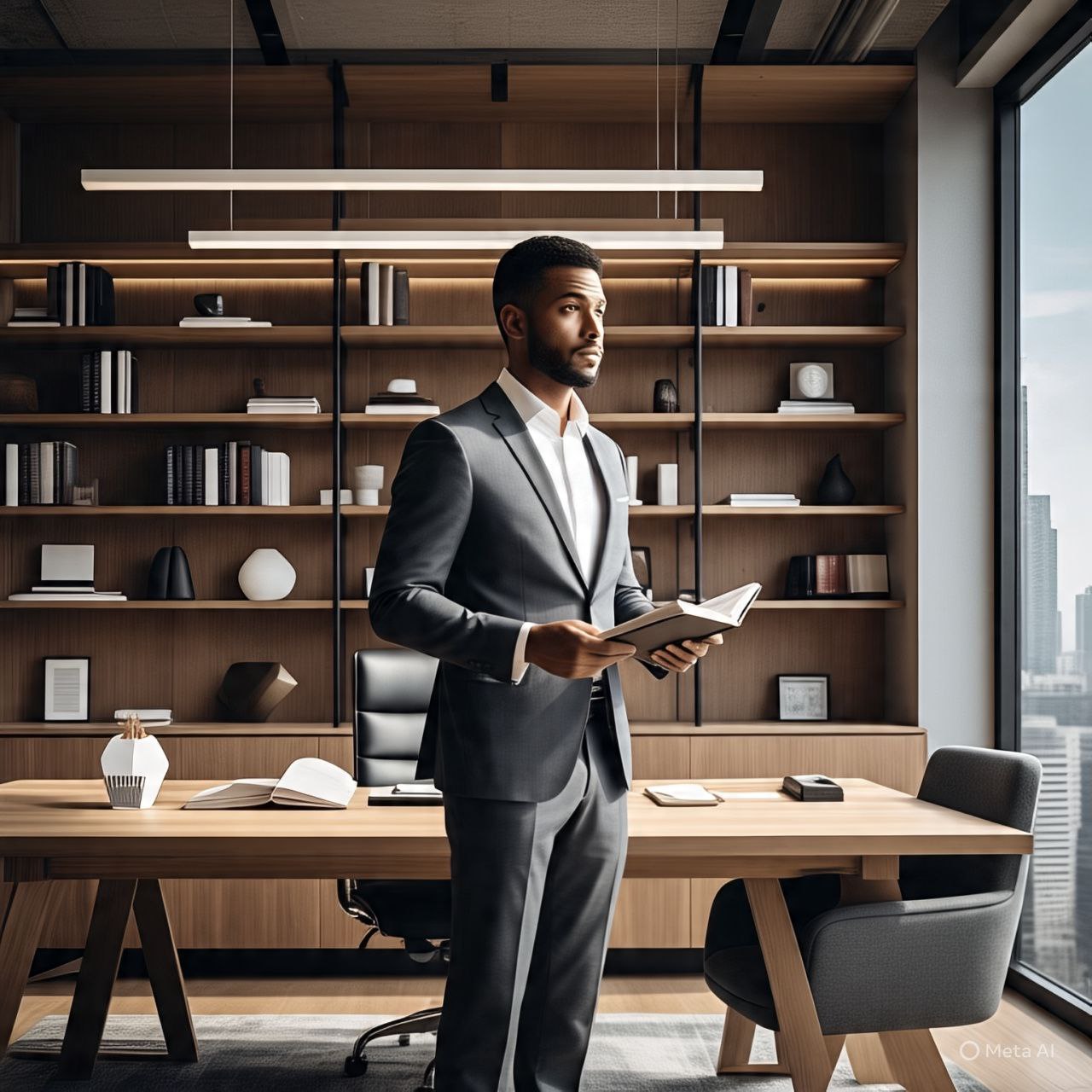
West is both an engineer and a construction manager with a solid ten-year track record in directing building projects and managing their financial aspects. Throughout his career, he has honed his skills in coordinating multidisciplinary teams, streamlining budget processes, and structuring financing plans that ensure projects are delivered on time and within financial targets.
Leave a Reply